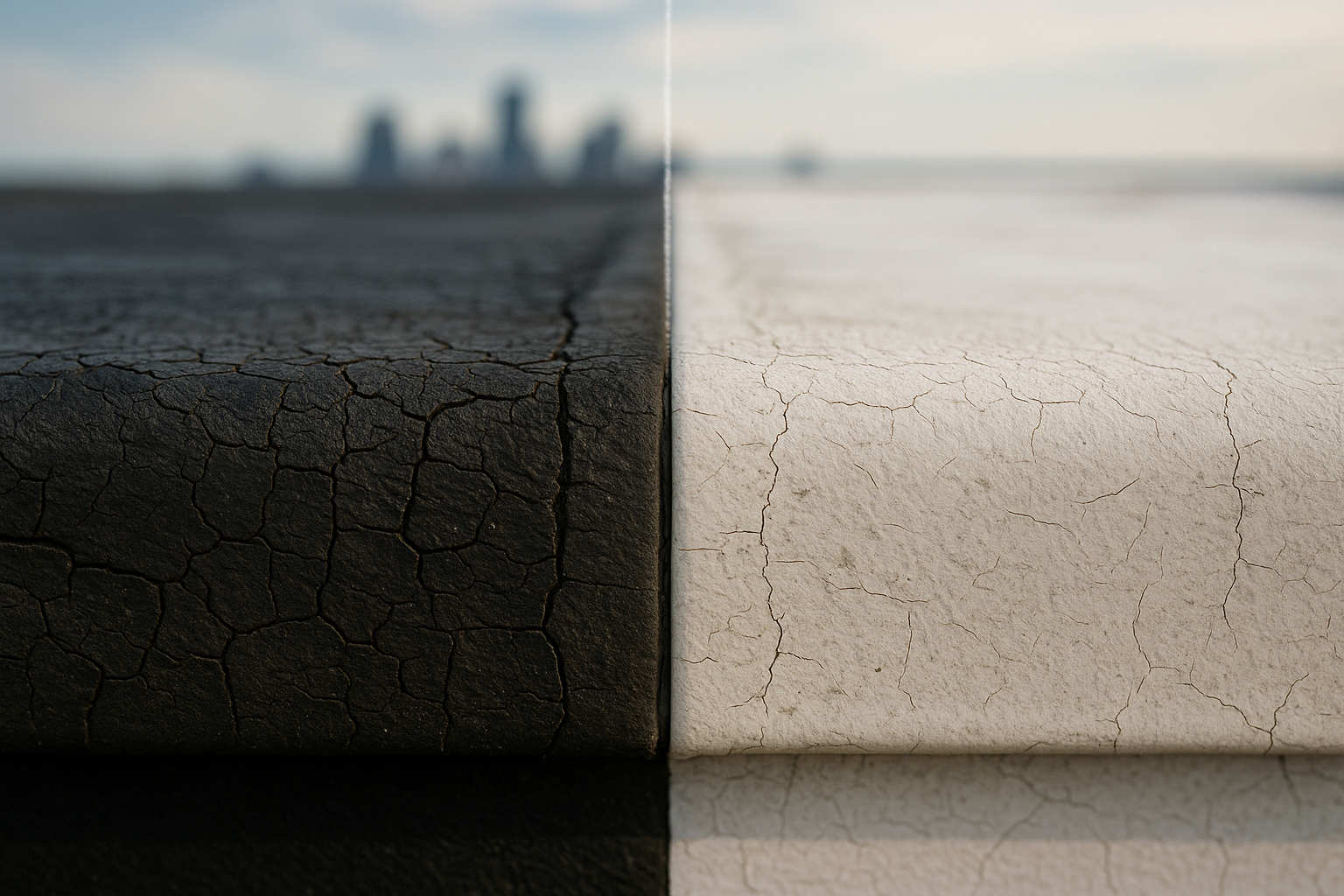
The Science of Membrane Aging: Why Some Roofs Survive and Others Fail
Bilal S.
Founder & CEO - BDR
Introduction
Let’s get something straight: not all roofs are created equal. You walk up to some 30-year-old buildings, peel back the top layer, and the roofing membrane is as tough as your business’s first failure. It is resilient and battle-tested. Others crack, split, and chalk; a couple bad seasons and they’re waving the white flag. The difference comes down to one thing: the science of membrane aging.
And if you don’t understand how membranes age, you’re gambling with your investment. What follows isn’t dry academia. Instead, these are principles distilled from decades of field data, lab tests, and innovation. If you want to stop buying new roofs every decade, read on.
Chemistry is Destiny: What’s in Your Roof?
Performance starts at the molecular level. Forget brands or flashy brochures. It’s about chemistry.
TPO: The Evolving Champion
Thermoplastic Polyolefin (TPO) is the newcomer, but it’s no rookie. At its core, it’s a blend: polypropylene and polyethylene, fused in sophisticated ways (reactor-blended, physically mixed). Add titanium dioxide, antioxidants, flame retardants, and you have a roof engineered to take abuse.
But this isn’t a kitchen recipe. Every additive is a double-edged sword:
- Titanium dioxide shields against UV. However, if it is unpassivated, it turns from friend to foe and catalyzes breakdown.
- Antioxidants (like Irgafos® 168, Irganox® 1010) provide protection by catching radicals and suppressing degradation, but only as long as they are present. Once depleted, the decline accelerates.
TPO’s superpower is its thermoplastic nature, which allows for heat-weldable seams that create airtight, watertight barriers. But as you’ll see, chemistry is only the first battleground.
EPDM: The Old Guard
Synthetic rubber, ethylene, propylene, diene monomer (EPDM). Sound familiar? It should. These membranes are studded with up to 40% carbon black.
Why? Because carbon black absorbs UV like a black hole. Without carbon black, the sun wins fast. That is why white EPDM, which lacks it, ages worse. The rest, including extending oils, curatives, and fillers, deal with stretch, toughness, and how the roof “feels” on impact.
The trade-off? EPDM isn’t heat weldable. Adhesion relies on tapes or solvents, which are only as good as the installer and the gods of chemistry.
The Brutal Truth of UV and Weather: How Degradation Happens
Think your roof just sits there passively? Think again. UV, water, and oxygen are relentless enemies.
TPO: Surface Wars
UV light yanks electrons from chemical bonds, kicking off a chain reaction in which free radicals tear apart the structure, creating carbonyl groups and embrittlement. Titanium dioxide tries to block the assault, and HALS (hindered amine light stabilizers) play clean-up, but the process never stops. When additives leach out or are consumed, surface cracks and discoloration accelerate the breakdown.
Add dirt and algae? It’s like putting salt in the wound, because moisture gets trapped and more reactions occur. Still, TPO has an ace: no plasticizer migration (unlike PVC). Stability is baked in, until it isn’t.
EPDM: Resilience Engineered In
Here, UV attacks ethylene and propylene parts, making hydroperoxides, then carbonyls. This is classic oxidative aging. But carbon black absorbs most UV, taking the bullet for the polymer. Surface crazing and shrinkage once plagued older formulas (blame plasticizer loss), but modern chemistry does better.
Remember: white EPDM, without this shield, crumbles quickly. EPDM’s main Achilles’ heel? Seams. The surface is so inert that adhesives can’t always bite.
Accelerated Aging? Simulate Hell, Predict Reality
Here’s the trick: you don’t have 30 years to wait for answers. So, we simulate decades in weeks using accelerated aging by turning up the heat, UV, and moisture. This pushes membranes to failure so fast it’s almost unfair.
- Heat (70°C+) speeds up oxidation.
- UV (xenon arc, carbon arc, fluorescent lamps) hammers chemical bonds.
- Moisture (condensation, spray) swells and stresses the material.
- Load (physical stress) tests for real-world abuse, such as punctures and seam splits.
Measurement matters:
- Energy-to-break (the area under a strain curve) is the real test of resilience. The more energy absorbed before failure, the better.
- Carbonyl index (via FTIR) reveals how much oxidation has happened. This is great for some membranes, but unreliable for others like EPDM and PVC.
But all these lab tests are only valuable if they match up with reality. So they get calibrated with real roofs, from humid South Florida to arid Arizona, spanning 12, 20, and 30-year-old roofs.
Field Learnings: The Inside Scoop from the Lab Bench and Jobsite
Insiders know the devil’s in the details. Here’s what top scientists and manufacturers are learning:
- Carbon black in EPDM isn’t optional; without it, service life plummets.
- Early TPOs failed not because TPO is bad, but because of dumb choices such as brominated flame retardants that broke down prematurely. Now, magnesium hydroxide and smarter stabilizers extend life.
- Greener additives aren’t just marketing; lignin-TPO blends, Vitamin E antioxidants can cut health hazards and maybe extend performance.
- Welding TPO is an art. If it is too hot, too fast, or too narrow, seams fail. The sweet spot is 400 to 450°C, at 2 m/min, with a seam width over 0.5 inches.
- Self-healing membranes are becoming real. Imagine a roof that fixes micro-damage, triggered by sunlight. This isn’t science fiction anymore.
- Even the best chemistry can be undone by bad installation. For instance, moisture and dirt at seams, under-cured adhesives, or poorly controlled fastener detailing can all cause problems.
Direct Comparison: EPDM vs. TPO
Numbers and charts matter, but here’s the distilled truth from decades of data.
| Property / Scenario | EPDM | TPO | |------------------------|--------------------------------------------------------|---------------------------------------------------| | UV & ozone resistance | Outstanding (thanks to carbon black) | Good (depends on UV stabilizer package) | | Durability | 30+ years possible; mechanical retention stays high | Solid long-term if kept cool and UV-protected | | Key vulnerabilities | Seam adhesion, shrinkage (old versions), water uptake | Cap layer erosion, seam quality, additive loss | | Energy efficiency | Low (black absorbs heat) | High (white reflects heat) | | Installation | Taped or solvent-adhered seams | Heat-welded, forming a monolithic sheet | | Repairability | Good, but new adhesive surfaces can be tricky | Excellent, especially with re-welding |
Both can exceed ASTM standards years after install, but only if initial chemistry and installation are right.
Installation: Where the Game is Won or Lost
No membrane survives installer incompetence.
- TPO’s strength is in its welded seams; however, welding requires precision.
- EPDM needs perfect surface prep for seams because adhesives must get molecular access.
- Mechanical attachment brings its own risks: fastener pull-out and membrane tearing. Fully adhered systems are tighter, but only if every step is perfect.
Bottom line? The best membrane, badly installed, fails faster than the cheapest one, installed right.
Wrapping Up: Outlasting the Clock
Aging in roofing isn’t fate; it’s a series of decisions, from chemistry to installation to additive packages.
TPO and EPDM both can last decades. But one resists the sun and ozone by absorbing punishment (carbon black in EPDM), while the other reflects and blocks damage (TPO, with UV absorbers and antioxidants).
Failures tend to start where control is lost: at seams and fasteners, or when the antioxidant barrier is breached.
The future? Greener, smarter membranes and maybe even self-healing roofs are on the horizon. But one rule stands: understand the science, control the process, and your roof will survive while others fail.
References
- Bailey, D. M., Cash, C. G., & Davies, A. G. (2002). Predictive Service Life Tests for Roofing Membranes: Phase II Investigation of Accelerated Aging Tests for Tracking Degradation of Roofing Membrane Materials (ERDC/CERL TR-02-22). U.S. Army Engineer Research and Development Center.
- Cash, C. G., & Bailey, D. M. (1994). Predictive Service Life Tests for Roofing Membranes: Phase 1 (USACERL Interim Report FM-94/03). U.S. Army Construction Engineering Research Laboratories.
- Hutchinson, T. W. (2015). An ERA Study Proves EPDM Easily Lasts More than 30 Years. EPDM Roofing Association.
- Keegan, J., Taylor, T. J., & Kirby, J. R. (2020). Proven Performance: Aged TPO Field Study. XV International Conference on Durability of Building Materials and Components, DBMC 2020, Barcelona.
- Hamilton, J., Klass, S., Mizuno, H., & Tsou, K. (2018). Greener Solutions for Thermoplastic Polyolefin Polymer Membrane Roofing Additives. University of California, Berkeley.
- Simmons, T. R., Runyan, D., Liu, K. K. Y., Paroli, R. M., Delgado, A. H., & Irwin, J. D. (1999). Effects of Welding Parameters on Seam Strength of Thermoplastic Polyolefin (TPO) Roofing Membranes. Proceedings of the North American Conference on Roofing Technology.
- Pierce, H. H., & Xing, L. (2017). Understanding Accelerated UV, Field and Thermal Aging of Thermoplastic Roofing Membranes. XIV DMBC 2017.
- Ackermann, H., Schönbrodt, S., Kerber, C., & Rokamp, R. (2024). Self-adhering sealing device with an adhesive sealant layer. US Patent No. 11,945,983 B2.